Understanding Pneumatic Valve Fundamentals
Core Components and Operation
Pneumatic valves are essential devices used to control fluid flow in various industrial applications. They consist of main components such as the actuator, body, seat, and stem. These components work together harmoniously: the actuator powers the valve by converting air pressure into mechanical movement, which positions the stem to engage or disengage the seat within the valve body, allowing or blocking fluid flow. Understanding how air pressure influences pneumatic valves is crucial; increased pressure can enhance valve operation by ensuring precise control over fluid dynamics. Moreover, a fundamental grasp of physics is vital, including pressure and flow dynamics, as these principles govern the efficient and reliable functioning of pneumatic valves under diverse conditions.
Types of Pneumatic Valves and Their Applications
Pneumatic valves come in several types, each tailored for specific applications. Common types include Solenoid Valves, which electronically control the fluid flow; ball valves, known for their robust and reliable sealing; and butterfly valves, favored for their compact design and quick operation. For instance, solenoid valves are widely used in automation systems due to their precision and ease of integration. Ball valves are preferred in manufacturing for their durability and capacity to handle high pressures, while butterfly valves are ideal for low-pressure applications requiring fast actuation. Each type has its advantages and drawbacks; solenoid valves offer excellent efficiency but may require regular maintenance, whereas ball valves boast reliability but are less suitable for fluid throttling. Industry reports suggest a growing trend toward butterfly valves due to their streamlined design and cost-effectiveness. Understanding these types and their respective applications helps businesses choose the right valve for their operational needs, enhancing efficiency and reliability in fluid control systems.
Proper Installation Techniques
Pre-Installation Checks and Environment Setup
Before installing a pneumatic valve, it is essential to carry out several pre-installation checks to ensure compatibility with the existing system. This involves verifying that the valve meets required pressure ratings and matches the system specifications. A clean work environment is crucial, as it helps prevent contamination that could affect valve performance. Preparing the necessary tools and materials in advance is also vital to streamline the installation process and ensure efficiency.
Step-by-Step Installation Process
Installing a pneumatic valve requires careful attention to detail and adherence to safety precautions. Follow these steps for a successful installation:
- Safety First: Begin by reviewing safety protocols and wearing appropriate protective gear.
- Inspect the Valve: Examine the valve and accessories for any damage or defects.
- Position the Valve: Determine the correct installation orientation according to manufacturer guidelines.
- Attach the Valve: Secure the valve to the system using the recommended method, ensuring seals are tight.
- Connect Pneumatic Links: Connect the pneumatic lines, ensuring there are no leaks.
- Test the System: Once installed, run preliminary tests to assess valve functionality.
- Troubleshooting: Identify and resolve any issues, referring to manufacturer instructions as needed.
Avoid common pitfalls, such as neglecting the manufacturer guidelines or overlooking connection leaks, as these can lead to improper valve function. Following these step-by-step instructions and remaining attentive to potential errors ensures a high-performing pneumatic valve installation.
Effective Operation Procedures
Starting, Adjusting, and Stopping Valves
Proper operation procedures are vital for ensuring the safe and efficient performance of pneumatic valves. The correct method to start, stop, and adjust these valves begins with understanding the specific controls and safety mechanisms each valve is equipped with. Operators must activate valves in a controlled manner, allowing systems to stabilize before making any adjustments or halts. Monitoring and fine-tuning valve settings is necessary to maintain optimal performance, ensuring pressures and flows are within operational limits. Training for operators is crucial to minimize errors and reduce the risk of malfunctions, as well-versed operators can better handle the nuances of the pneumatic systems they're managing.
Optimizing Pressure and Flow Settings
Optimizing pressure and flow settings is essential for the efficient operation and longevity of pneumatic systems. Proper settings can lead to increased productivity and reduced energy consumption. Testing and adjusting these settings effectively involve benchmarking standard performance criteria and making precise modifications based on real-time data. Case studies highlight the significant impact of optimized settings; for instance, one study demonstrated a 20% increase in operational efficiency after re-calibrating pressure settings in a manufacturing setup. These examples underscore the value of diligent pressure and flow optimization, ensuring systems operate at their peak while reducing unnecessary strain.
Scheduled Maintenance Tasks
Conducting regular maintenance tasks is crucial for ensuring the longevity of pneumatic valves. Key tasks include inspecting for wear, checking seals, and testing valve responses to ensure they function optimally. Maintaining a comprehensive log of these tasks is equally important, as it helps track performance and schedule future checks based on historical data. For instance, manufacturers often recommend routine inspections every three to six months, depending on valve usage intensity and operating conditions. Following these guidelines can prevent unexpected failures and extend the operational life of the valves.
Lubrication and Component Replacement
Proper lubrication is essential for the efficient operation of pneumatic valves. Choosing the right lubricants, such as silicone-based options, can significantly reduce friction and wear. This minimizes the risk of common failures and enhances valve performance. It's also important to know when to replace components; indicators like abnormal noise or reduced performance can be signs that parts are due for replacement. By adhering to best practices, like applying lubricant regularly and monitoring for wear, operators can maintain valves in peak condition, ensuring reliable performance.
Avoiding Common Usage Errors
Incorrect Valve Selection and Sizing
Using the wrong type or size of pneumatic valve can lead to several detrimental consequences, including reduced system efficiency and increased operational costs. The selection of the appropriate valve should be based on specific application criteria such as pressure requirements, flow rates, and environmental conditions. For instance, selecting a valve with too low a flow rate can constrict air passage, while incorrect sizing can cause excessive wear and energy consumption. A fitting example is Emerson's AVENTICSTM Series XV pneumatic valves, which offer high flow rates and flexible configurations suitable for varied automation solutions. Incorrect selection could lead to premature system failures and unnecessary financial expenditures, underscoring the necessity of informed decision-making in valve specification.
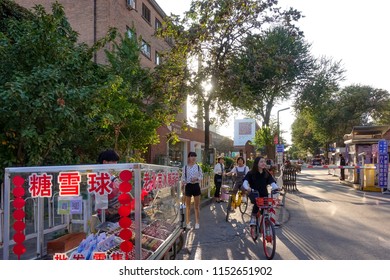
Neglecting Maintenance and Safety Checks
Neglecting maintenance and safety checks for pneumatic valves can expose systems to risks such as operational inefficiencies and unexpected breakdowns. Regular inspections are pivotal in identifying potential issues before they escalate into serious failures. Industry experts suggest that routine maintenance significantly bolsters operational safety and reliability, aligning with the practices recommended by Emerson in their pneumatic valve systems. Data indicates that frequent assessments correlate positively with enhanced longevity and performance of pneumatic valves, as emphasized in Emerson's safety certifications for the Series XV valves. Committed adherence to maintenance schedules not only ensures efficient valve function but also minimizes the risk of safety hazards, making it an essential practice for optimal system operation.
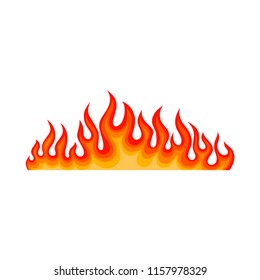
For instance, Emerson's pneumatic valve systems incorporate UL certifications to ensure compliance with quality and safety standards—a testament to the vital role regular inspections play in safeguarding operational integrity. Through routine checks, operators can preemptively address wear and potential malfunctions, thereby fostering a secure operating environment and reducing operational downtime.
Safety and Emergency Protocols
Safe Handling and Operation Guidelines
Proper handling and operation of pneumatic valves are crucial for ensuring workplace safety and preventing accidents. Employees should adhere to specific safety guidelines, such as wearing appropriate personal protective equipment (PPE) and using the correct tools designed for pneumatic systems. Training programs are essential for instilling safe practices specific to the operation of pneumatic valves. These programs should cover identifying potential hazards, safe operation techniques, and emergency procedures. Additionally, compliance with both international and local safety standards and regulations, such as the ISO standards for industrial valve safety, should be strictly followed. Companies that prioritize these measures not only protect their workforce but also improve operational efficiency and reliability.
Responding to Malfunctions and Emergencies
Developing a robust protocol for responding to pneumatic valve malfunctions is crucial to maintaining safety and minimizing downtime. In the event of a malfunction, operators should immediately follow a systematic procedure that includes shutting down the valve system, inspecting it for visible issues, and consulting the manufacturer's troubleshooting guide. Emergency situations, such as a sudden system failure, require a well-established evacuation protocol to ensure all personnel can safely exit the area. Regularly conducting emergency drills prepares staff to act efficiently during real crises, reinforcing their ability to respond promptly and effectively. Incorporating such protocols ensures not only the safety of employees but also the protection of equipment and resources.